Mon, 03 Feb 2025 10:46:17 +0100
Inert Gas) welding has established itself as the best option to guarantee strong, precise and highly resistant joints. Its application is not limited only to aeronautics, but also extends to industrial sectors such as the manufacture of ultrasonic cleaning machines, where structural quality is key to the efficiency and durability of the equipment.
Discover in this blog aeronautical quality TIG welding, its benefits and advantages, and how its application in DCM Ultrasonic ultrasonic cleaning machines represents an indisputable competitive advantage in the market.
In the aeronautical sector, safety and structural reliability are fundamental aspects, which makes TIG welding the preferred technique for working with critical materials such as:
High Precision and Control
TIG welding allows precise control of the electric arc and the application of the filler material, which reduces defects such as porosities or inclusions.
High Quality Joints
Due to inert gas shielding, the resulting weld is contaminant-free and highly resistant to oxidation.
Versatility in Materials
It is applicable to a wide range of metals, including stainless steels, aluminum, copper and titanium.
Spatter and Residue Reduction
Unlike other welding processes, TIG does not generate slag or spatter, making cleaning and final finishing easier.
Excellent Weld Aesthetics
TIG welding produces clean, uniform joints, essential for applications where appearance is also a relevant factor.
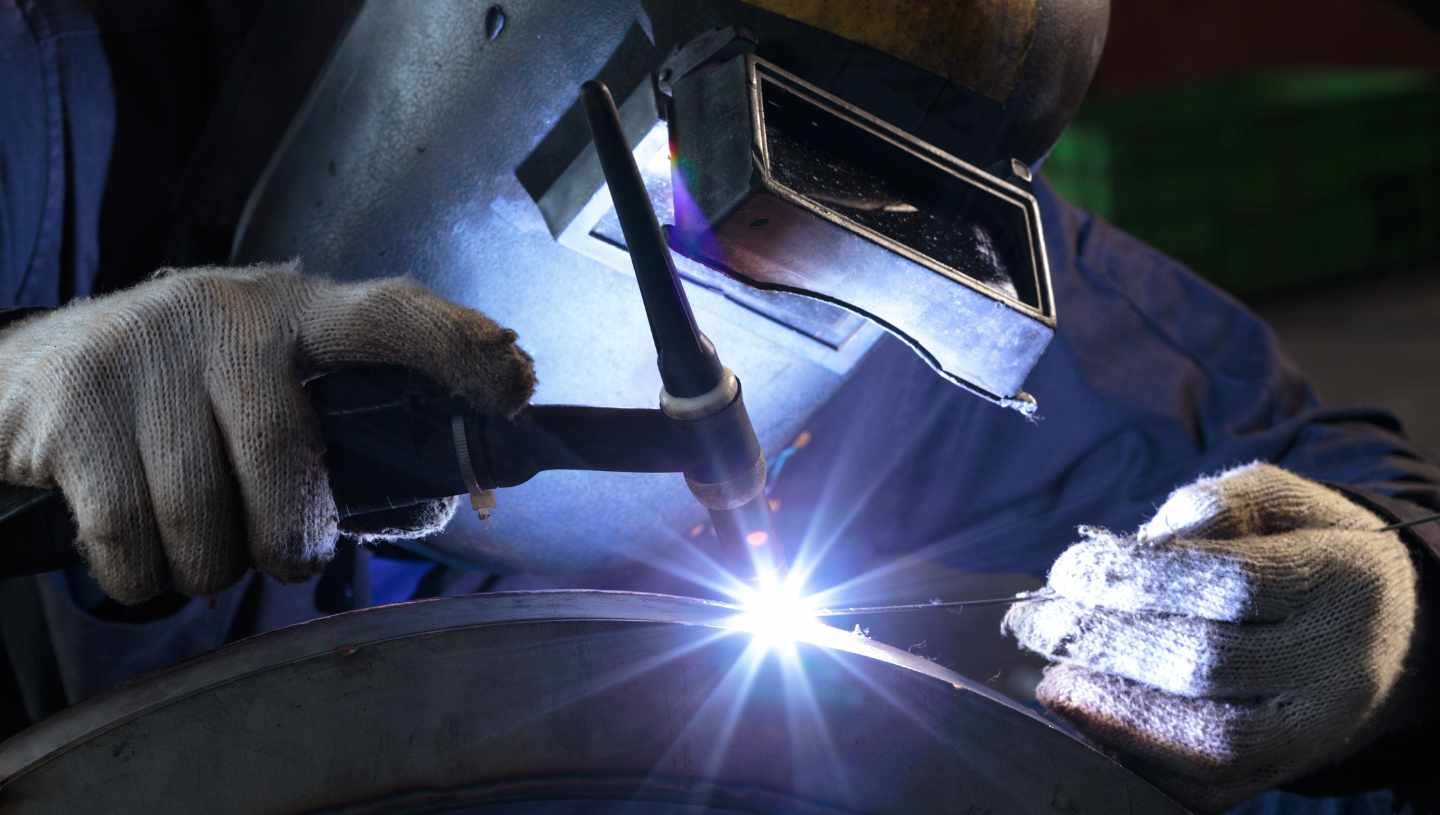
Ultrasonic cleaning machines are subject to demanding conditions, including exposure to chemicals, elevated temperatures and constant ultrasonic vibrations. The structural integrity of their components is essential to ensure their performance and durability.
Advantages of TIG Welding in Ultrasonic Cleaning Equipment
At DCM Ultrasonic, we apply aircraft-grade TIG welding in the manufacture of our ultrasonic cleaning machines. This allows us to offer equipment with a superior level of quality, characterized by:
TIG welding is a fundamental process in the manufacture of industrial equipment that requires high strength, precision and durability. In the ultrasonic cleaning industry, its application guarantees robust, hermetic and highly efficient structures.
At DCM Ultrasonic, we have integrated this technology with aeronautical quality standards, ensuring that our ultrasonic cleaning machines are synonymous with reliability, efficiency and excellence. Also, if you need to apply this welding to your industrial machines, you can contact the services of DCM Mechanical Engineering.
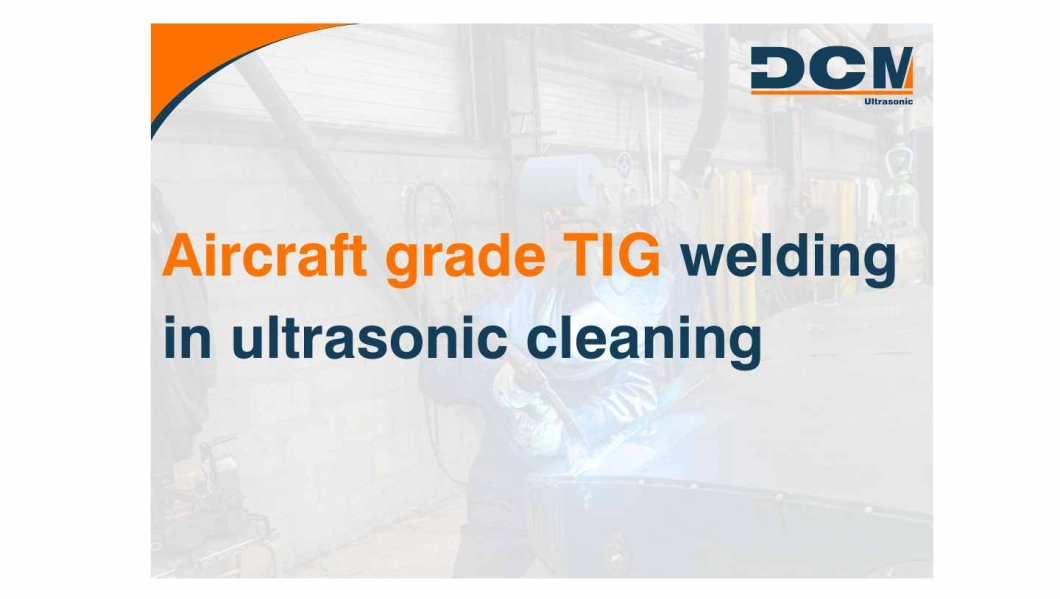
News
Aeronautical Quality TIG Welding
03 February de 2025
The aeronautical industry demands the highest quality standards in each of its manufacturing and assembly processes. Among these processes, TIG (TungstenInert Gas) welding has established itself as the best option to guarantee strong, precise and highly resistant joints. Its application is not limited only to aeronautics, but also extends to industrial sectors such as the manufacture of ultrasonic cleaning machines, where structural quality is key to the efficiency and durability of the equipment.
Discover in this blog aeronautical quality TIG welding, its benefits and advantages, and how its application in DCM Ultrasonic ultrasonic cleaning machines represents an indisputable competitive advantage in the market.
What is TIG Welding and why is it key in aeronautical applications
TIG welding is an electric arc welding process in which a non-consumable tungsten electrode and an inert gas, usually argon or helium, are used to protect the weld from oxidation and contamination. It is characterized by its high precision and by generating high-quality joints with excellent mechanical and thermal resistance.In the aeronautical sector, safety and structural reliability are fundamental aspects, which makes TIG welding the preferred technique for working with critical materials such as:
- Aluminium alloys: used in fuselages and structural components.
- Titanium: present in engines and parts subjected to high temperatures.
- Stainless steels and superalloys: for hydraulic and exhaust systems.
- Strict quality controls in the aeronautical industry ensure that welded joints are highly resistant to fatigue, vibrations and corrosion, essential characteristics for maintaining safety in flight.
Benefits of TIG Welding in Industrial Applications
TIG welding presents a series of advantages that make it the ideal option for applications where quality and durability are a priority. Among its benefits are:High Precision and Control
TIG welding allows precise control of the electric arc and the application of the filler material, which reduces defects such as porosities or inclusions.
High Quality Joints
Due to inert gas shielding, the resulting weld is contaminant-free and highly resistant to oxidation.
Versatility in Materials
It is applicable to a wide range of metals, including stainless steels, aluminum, copper and titanium.
Spatter and Residue Reduction
Unlike other welding processes, TIG does not generate slag or spatter, making cleaning and final finishing easier.
Excellent Weld Aesthetics
TIG welding produces clean, uniform joints, essential for applications where appearance is also a relevant factor.
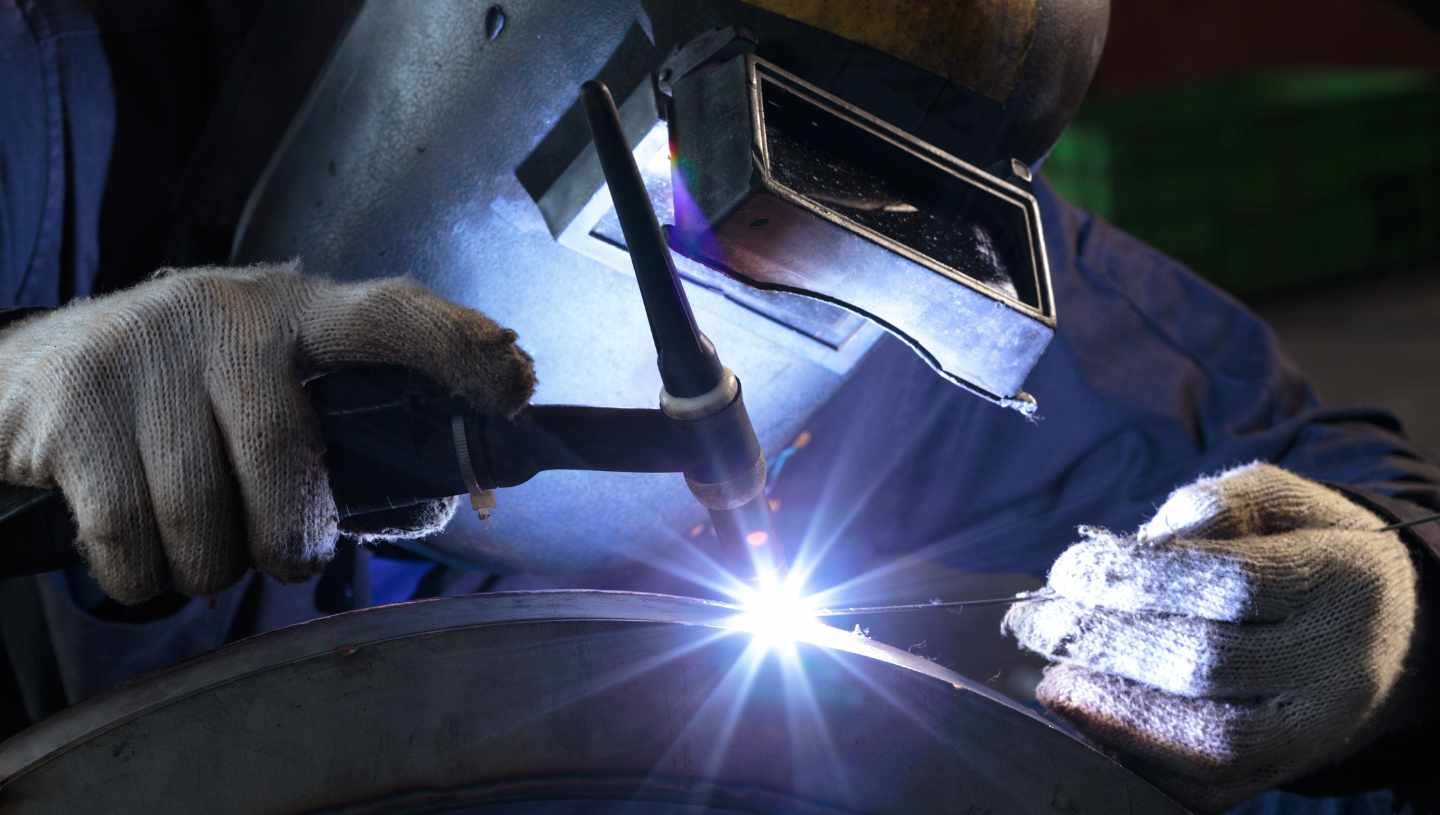
Application of TIG Welding in Ultrasonic Cleaning Machines
Ultrasonic cleaning machines are subject to demanding conditions, including exposure to chemicals, elevated temperatures and constant ultrasonic vibrations. The structural integrity of their components is essential to ensure their performance and durability.Advantages of TIG Welding in Ultrasonic Cleaning Equipment
- Robust and hermetic structure: The high quality of TIG joints allows for the manufacture of fully sealed stainless steel tanks, preventing liquid leaks and reducing premature wear.
- Greater resistance to corrosion: Thanks to the purity of the weld, the equipment better resists the chemical agents used in cleaning processes.
- Reduced maintenance: Defect-free welded joints minimize the risk of cracks or structural failures over time.
- Better transmission of ultrasonic vibrations: The structural continuity of TIG-welded tanks optimizes the propagation of ultrasonic waves, improving the efficiency of the cleaning process.
- Longer equipment life: The combination of quality construction and resistant materials guarantees long and reliable performance.
DCM Ultrasonic's Competitive Advantage
At DCM Ultrasonic, we apply aircraft-grade TIG welding in the manufacture of our ultrasonic cleaning machines. This allows us to offer equipment with a superior level of quality, characterized by:
- TIG-welded AISI 316L stainless steel tanks for exceptional resistance to chemical agents and extreme temperatures.
- Hermetically sealed structures, ensuring the safety and efficiency of the cleaning process.
- Optimized designs that maximize the propagation of ultrasonic waves for deep and uniform cleaning.
- The application of aircraft-grade welding standards in our equipment sets us apart from the competition and allows us to offer ultrasonic cleaning solutions with the highest reliability and durability on the market.
TIG welding is a fundamental process in the manufacture of industrial equipment that requires high strength, precision and durability. In the ultrasonic cleaning industry, its application guarantees robust, hermetic and highly efficient structures.
At DCM Ultrasonic, we have integrated this technology with aeronautical quality standards, ensuring that our ultrasonic cleaning machines are synonymous with reliability, efficiency and excellence. Also, if you need to apply this welding to your industrial machines, you can contact the services of DCM Mechanical Engineering.