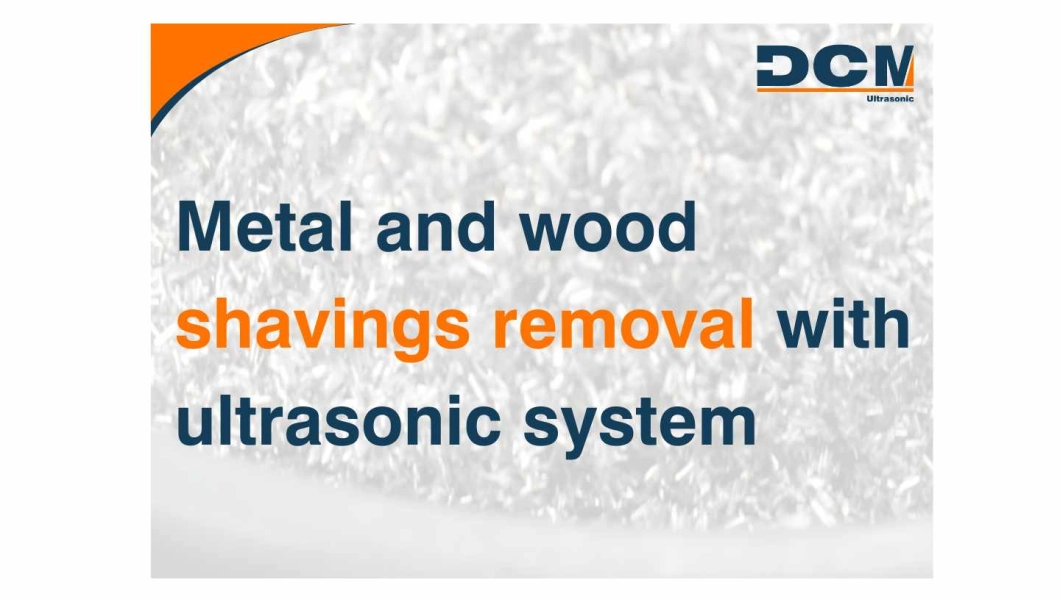
Metal shavings and wood shavings removal with ultrasound
The removal of industrial dust and machining residues is a critical challenge in the metalworking and manufacturing industry. These residues can affect the quality of the final product, compromise the functionality of the parts and reduce the efficiency of the production processes. Processes such as sawing, milling or drilling generate chips in many industries (wood industry, plastics industry and metallurgy). Ultrasonic cleaning machines have proven to be an effective solution for chips removal, ensuring deep cleaning without damaging the surfaces of the components.
Industrial dust removal - Metal shavings - Wood shavings
Machining chips vary depending on the material worked, the type of tool used and the cutting conditions. Among the main ones we find:
1. Continuous chips
-
They are generated in processes such as high-speed turning or milling.
-
They can adhere to the parts, making manual cleaning difficult.
2. Discontinuous Chips
-
Common in fragile materials or in interrupted machining.
-
They are deposited in cavities and crevices, requiring thorough cleaning.
3. Needle-shaped or Splinter-shaped Chips
-
Frequent in the machining of hard alloys and stainless steels.
-
They represent a risk of contamination and must be completely removed.
4. Spiral or Curly Chips
-
Produced in cutting processes with high feed rate.
-
Their complex geometry makes it difficult to extract them from blind holes and internal channels.
5. Aluminum and Light Alloy Chips
-
Softer and more malleable, but with a tendency to adhere to surfaces.
-
They require meticulous cleaning to avoid cross contamination.
SEE MACHINES FOR METAL AND WOOD SHAVINGS
How Ultrasonic Shavings Removal Works
Ultrasonic cleaning uses high-frequency waves to generate cavitation in a cleaning fluid. This phenomenon allows chips and adhering contaminants to be removed without the need for mechanical contact.
Cleaning Process
-
Piece Immersion: The parts are immersed in a tank with a specialized fluid.
-
Generation of Ultrasonic Waves: The transducers convert electrical energy into high-frequency sound waves.
-
Microbubble Formation: The waves create microbubbles that implode, generating microjets.
-
Chip Removal: The energy released dislodges and carries away the chips, even in hard-to-reach areas.
-
Fluid Filtration and Recycling: The cleaning fluid is filtered to remove residue and extend its useful life.
Advantages of Ultrasonic Chip Removal
1. Deep Cleaning
- Reaches complex geometries, blind holes and internal cavities.
- Guarantees the complete removal of microscopic residues.
2. Non-Abrasive Process
- Does not cause wear on parts.
- Preserves the structural integrity of sensitive components.
3. Greater Efficiency and Time Reduction
- Shorter cleaning time compared to manual methods.
- Compatible with automated production lines.
4. Reduced Chemical Consumption
- Minimizes the use of aggressive solvents.
- Less environmental impact and lower operating cost.
5. Better Quality and Regulatory Compliance
- Ensures the cleaning required in industries such as aerospace, automotive and medical.
- Complies with strict pollution and safety regulations.
Applications in Industry
Automotive Industry
Cleaning of engine blocks, heads, injectors and transmission components.
Removing chips from brake and steering systems.
Aerospace Industry
Decontamination of structural components and turbines.
Removing machining residues from high-precision parts.
Medical and Biomedical Devices Sector
Cleaning of orthopedic implants, surgical instruments and titanium components.
Mold and Die Industry
Removing machining residues and lubricants from mold cavities.
Extending the useful life of injection molds.
ASK US HOW YOU CAN REMOVE SHAVINGS FROM YOUR PARTS
Tips for efficient metal and wood shavings removal with your ultrasonic machine
- Select the Right Frequency: Low frequencies (20-40 kHz) for coarse contaminants and high frequencies (40-80 kHz) for delicate parts.
- Use an Appropriate Cleaning Fluid: Choose detergents compatible with the material and nature of the residue.
- Optimize Bath Temperature: Maintain between 50°C and 70°C to improve cavitation.
- Avoid Overloading the Tank: Ensure even distribution of parts for effective cleaning.
- Perform Periodic Maintenance: Check transducers and filter fluid regularly to ensure optimal performance.
DCM Ultrasonic: Advanced Chip Removal Solutions
At DCM Ultrasonic, we design and manufacture high-tech ultrasonic cleaning machines, specifically designed for chip removal in industrial processes. Our equipment stands out for:
- Optimized cavitation technology for deep and homogeneous cleaning.
- Dynamic loading systems that improve the distribution of the cleaning fluid.
- Reduction of operating costs through energy efficiency and lower chemical consumption.
- Customization of equipment according to the specific needs of each industry.
If you are looking for an efficient and reliable solution for removing chips using ultrasound, contact us and discover how our machines can optimize your production process.