Tue, 15 Apr 2025 11:32:58 +0200
Compared to conventional methods such as solvent cleaning, sandblasting, or aggressive chemical treatments, ultrasonic cleaning technology has established itself as an advanced, effective, non-invasive, and environmentally friendly solution, capable of adapting to the complexity of these materials without compromising their integrity.
As quality, sustainability, and precision requirements increase, ultrasound continues to position itself as the most advanced and versatile cleaning technology in the industrial market.
1. Deep cleaning in hard-to-reach areas
Ultrasonic cavitation can reach microcracks, internal channels, pores, and complex geometries that traditional methods cannot reach, ensuring thorough cleaning even on parts with intricate designs.
2. Non-abrasive and safe process
Unlike blasting, brushing, or aggressive chemical cleaning, ultrasound does not erode or damage surfaces, protecting technical finishes, functional coatings, and sensitive structures, especially in composite materials.
REQUEST INFORMATION ABOUT OUR ULTRASONIC SYSTEMS
3. Compatibility with a wide range of materials
The technology can be adjusted to specific frequencies, temperatures, and detergents, allowing cleaning of everything from light alloys (aluminum, magnesium) to carbon fiber or glass composites, without damaging the integrity of the material.
4. Significant reduction in time and costs
Thanks to its efficiency, ultrasonic cleaning reduces cycle times, direct labor usage, and the need for rework, resulting in increased productivity and profitability of the process.
5. Automatable and Repeatable Process
It is easily integrated into automated lines, with standardized and controllable parameters (temperature, time, frequency), ensuring consistent and repeatable results, key in demanding sectors such as aeronautics or medicine.
6. Sustainability and Low Environmental Impact
It reduces or eliminates the use of toxic solvents and harsh detergents.
It minimizes water and energy consumption thanks to insulation and recycling systems.
It generates less waste and emissions, helping to reduce the carbon footprint of industrial processes.
7. Improved Final Product Quality
Efficient cleaning improves the adhesion of paints, coatings, or heat treatments, reduces assembly failures, and improves overall product performance, especially in critical components.
8. High Application Versatility
A single ultrasonic system can be adapted to clean different types of materials and parts, from large metal blocks to delicate components, reducing the need for multiple pieces of equipment.
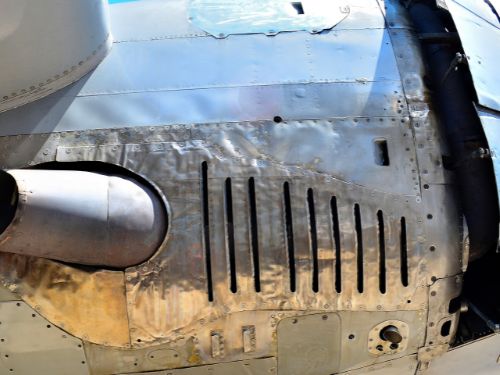
DISCOVER OUR INDUSTRIAL CLEANING MACHINES
Ultrasonic machines are ideal for cleaning parts made of composite materials and metal alloys!
At DCM Ultrasonic, we develop ultrasonic cleaning systems aimed at optimizing efficiency in the processing of high-performance composite materials and alloys. Thanks to their cutting-edge technology, our equipment significantly reduces cleaning times compared to conventional methods, removing contaminants quickly and consistently without the need for laborious disassembly. Furthermore, their energy-efficient design and reduced use of chemicals contribute to both reducing operating costs and protecting the environment.
DCM equipment is designed to be easily integrated into industrial production lines, improving work rates and facilitating maintenance. The automation and precision of the ultrasonic process prevent unnecessary wear on components, extending their useful life and reducing the frequency of costly replacements.
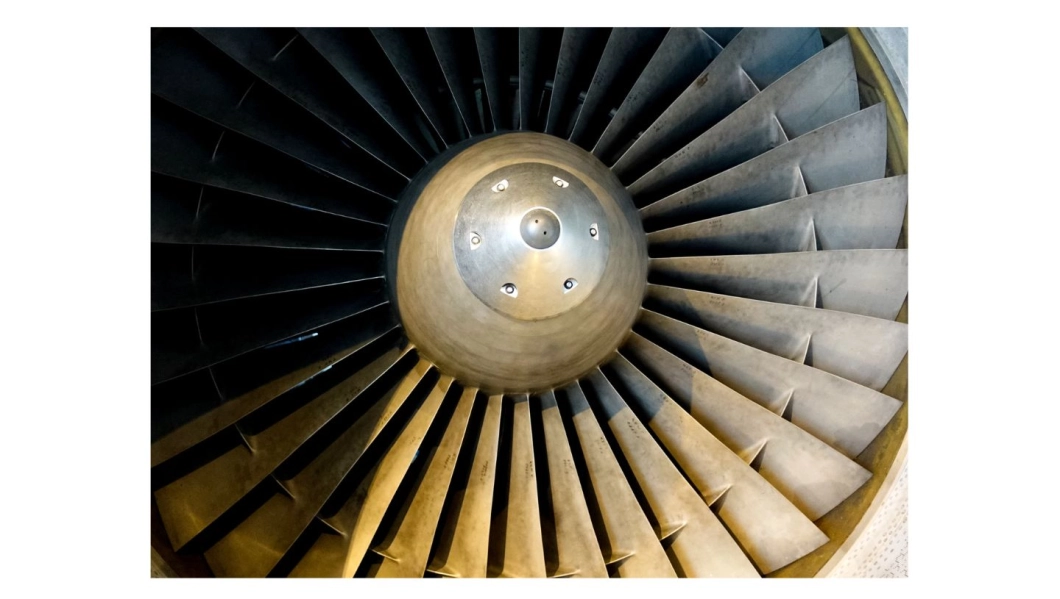
News
Industrial Ultrasonic Cleaning of Composite Materials and Metal Alloys
15 April de 2025
In modern industrial environments, the precise and efficient cleaning of components made of composite materials and metal alloys represents a key challenge. These materials, widely used in sectors such as aeronautics, automotive, energy, medicine, and heavy industry, require cleaning processes that ensure the preservation of their physical, mechanical, and structural properties.Compared to conventional methods such as solvent cleaning, sandblasting, or aggressive chemical treatments, ultrasonic cleaning technology has established itself as an advanced, effective, non-invasive, and environmentally friendly solution, capable of adapting to the complexity of these materials without compromising their integrity.
Industrial Cleaning of Composite Materials and Metal Alloys
Industrial ultrasonic cleaning of composite materials and metal alloys represents a safe, efficient, and environmentally friendly solution. Its adaptability to a wide variety of materials and sectors, along with its high performance and ease of integration into production lines, make it an essential tool for modern industry.As quality, sustainability, and precision requirements increase, ultrasound continues to position itself as the most advanced and versatile cleaning technology in the industrial market.
Why choose ultrasonic cleaning for cleaning composite materials and metal alloys?
Composite materials (such as carbon fibers, glass fibers, or reinforced epoxy resins) and metal alloys (such as those based on aluminum, titanium, magnesium, or nickel) have sensitive surfaces, complex geometries, and internal structures that make them difficult to clean using traditional methods. Ultrasonic cleaning offers multiple advantages in this context:1. Deep cleaning in hard-to-reach areas
Ultrasonic cavitation can reach microcracks, internal channels, pores, and complex geometries that traditional methods cannot reach, ensuring thorough cleaning even on parts with intricate designs.
2. Non-abrasive and safe process
Unlike blasting, brushing, or aggressive chemical cleaning, ultrasound does not erode or damage surfaces, protecting technical finishes, functional coatings, and sensitive structures, especially in composite materials.
REQUEST INFORMATION ABOUT OUR ULTRASONIC SYSTEMS
3. Compatibility with a wide range of materials
The technology can be adjusted to specific frequencies, temperatures, and detergents, allowing cleaning of everything from light alloys (aluminum, magnesium) to carbon fiber or glass composites, without damaging the integrity of the material.
4. Significant reduction in time and costs
Thanks to its efficiency, ultrasonic cleaning reduces cycle times, direct labor usage, and the need for rework, resulting in increased productivity and profitability of the process.
5. Automatable and Repeatable Process
It is easily integrated into automated lines, with standardized and controllable parameters (temperature, time, frequency), ensuring consistent and repeatable results, key in demanding sectors such as aeronautics or medicine.
6. Sustainability and Low Environmental Impact
It reduces or eliminates the use of toxic solvents and harsh detergents.
It minimizes water and energy consumption thanks to insulation and recycling systems.
It generates less waste and emissions, helping to reduce the carbon footprint of industrial processes.
7. Improved Final Product Quality
Efficient cleaning improves the adhesion of paints, coatings, or heat treatments, reduces assembly failures, and improves overall product performance, especially in critical components.
8. High Application Versatility
A single ultrasonic system can be adapted to clean different types of materials and parts, from large metal blocks to delicate components, reducing the need for multiple pieces of equipment.
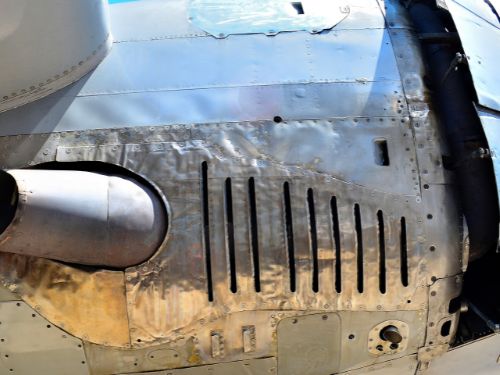
DISCOVER OUR INDUSTRIAL CLEANING MACHINES
Reduce costs and save cleaning time with our industrial ultrasonic cleaning machines.
Ultrasonic machines are ideal for cleaning parts made of composite materials and metal alloys!At DCM Ultrasonic, we develop ultrasonic cleaning systems aimed at optimizing efficiency in the processing of high-performance composite materials and alloys. Thanks to their cutting-edge technology, our equipment significantly reduces cleaning times compared to conventional methods, removing contaminants quickly and consistently without the need for laborious disassembly. Furthermore, their energy-efficient design and reduced use of chemicals contribute to both reducing operating costs and protecting the environment.
DCM equipment is designed to be easily integrated into industrial production lines, improving work rates and facilitating maintenance. The automation and precision of the ultrasonic process prevent unnecessary wear on components, extending their useful life and reducing the frequency of costly replacements.